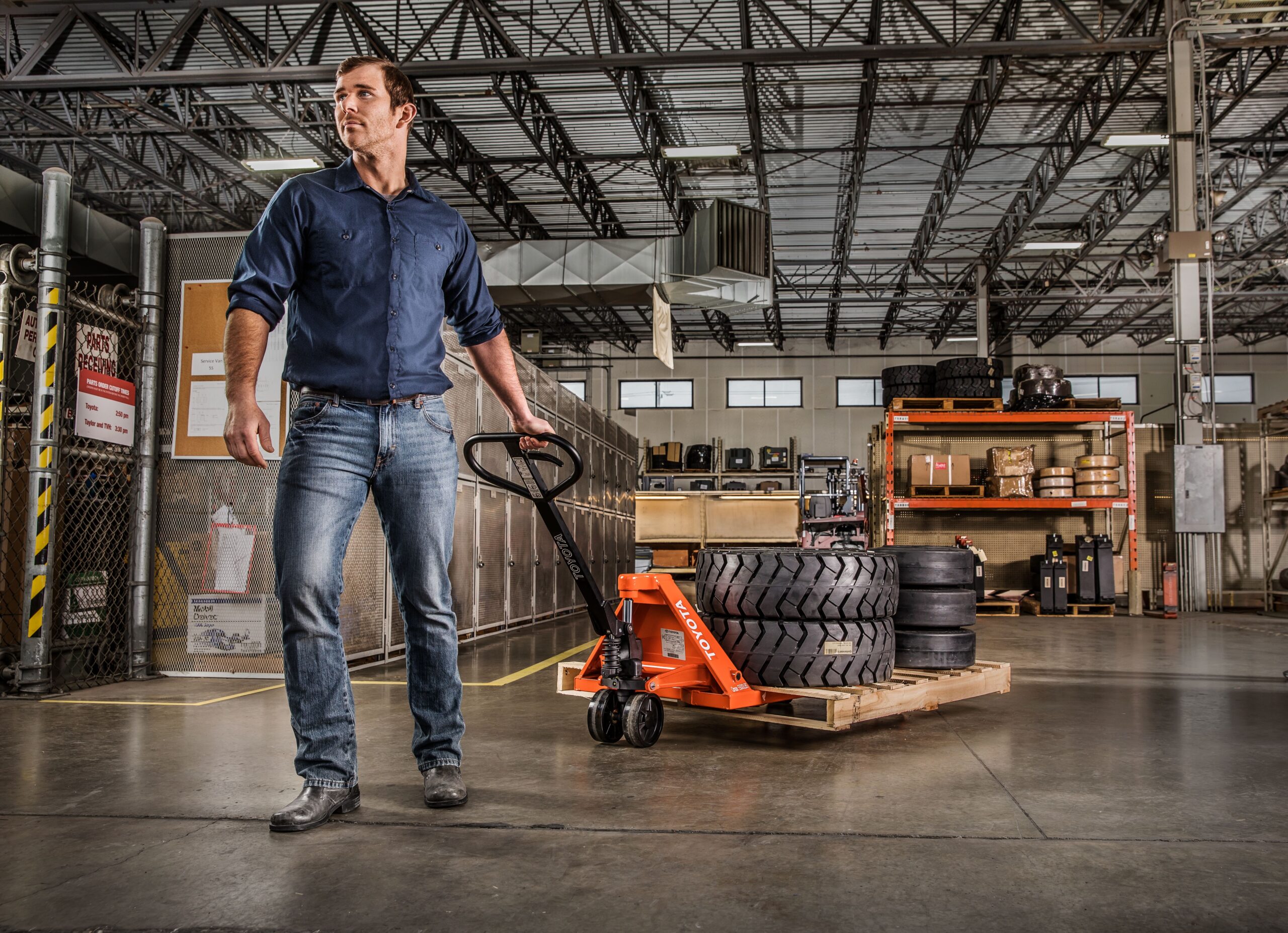
A basic hydraulic pump that can be operated by hand, a pair of steel tines set apart to accommodate either standard pallets from an organization like CHEP or export pallets, and a tiller arm for steering are all that is required to transform a single worker into a Hercules capable of single-handedly moving loads of two tones with minimal effort.
It is a valuable capability in Australia, given the long supply chains and high labour costs that command every fraction of a second of efficiency. Reliable Pallet jacks Brisbane suppliers are keeping retail, food-service and manufacturing customers in full swing, 24/7, in the busy distribution hubs of Port of Brisbane. The pallet jack is equalizer, with its compact size, low capital cost and almost zero licensing requirements — a corner convenience store and a multinational 3PL can move goods the same way. Dozens of incremental improvements—stainless-steel frames for wet zones, lithium-ion batteries for around-the-clock operations, and telematics for visibility through the fleet—have kept this humble workhorse current, even as robotic shuttles and automated cranes steal the spotlight. Any manager of a retail or warehouse outlet who wants to keep surf flowing and profitable needs to understand the origins, construction, and optimal operations of pallet jacks.
Evolution of Pallet-Handling Equipment
Freight used to move in wooden crates, burlap bags, and boxes hand-stacked one-by-one—a backbreaking, injury-prone procedure. When the wooden pallet entered the scene in the 1920s it had a huge impact on transportation — unfortunately, it also introduced a new problem: how would one move palletized loads quickly without cranes or draft animals? First low-lift trucks with mechanical jacks first showed up in American railyards, but it was the 1940s innovation of the hydraulic pump-handle design that opened up the gates to productivity.
Anatomy of a Pallet Jack
Peel the paint away and what you have is a surprisingly sophisticated piece of machinery. Laser-cut from high-tensile plate, with robot welding for consistency, then blasted and coated to prevent chip phobia. Within the pump cartridge, every time the operator “pumps” on the tiller handle, a small piston pushes hydraulic oil into a lift cylinder. The pressurized valve prevents over-lifting, protect both mechanism and merchandise. Each fork tip is equipped with entry rollers to direct the tines into pallet openings, while a nylon, polyurethane, or rubber load wheel bears the load. Poly wheels are quiet on polished concrete; nylon rolls well on bitumen but passes more shock; polyurethane is an intersection of both. Electric variants are outfitted with a sealed traction motor, gearing, and an AGM or lithium-ion pack that hot-swaps in seconds. The control heads include forward/reverse throttles, horn buttons and “creep” speed selectors for tight aisles. On select premium units, built-in LCD diagnostics that show lift counts, fault codes, and scheduled maintenance reminders are also featured. But even the fanciest walkie has that same fundamental geometry as a $600 manual jack: standard fork length, lowered height, and tapered tips tuned (via the Australian pallet standard) for a fit to ensure clear passage under the last-in, best-out core asset for any distribution centre, the pallet.
Final thoughts
Looking into the future, one can predict that low-cost electric drive units might transform manual Platform trolleys into semi-autonomous carts. For instance, prototype swarm-logic algorithms can already allow multiple trolleys to follow a picker like ducklings, using step ladders to keep their three-metre spacing. At the same time, edge-mounted cameras can verify barcode data instantly, meaning that the trolley is being used not for transportation alone but as a mobile scanning station. Furthermore, the wheels can harvest energy from the trolley’s motion, converting kinetic energy into a trickle charge for the onboard sensors instead of the previous requirement for overnight plugs. In other developments, augmented-reality visors can project the directions for every batch item, ensuring that the picker knows which direction to walk and glance for the pick-up destination.